- Home
- Symmetry Blog
- 14 Trends Driving Smart Manufacturing
14 Trends Driving Smart Manufacturing
About Jari Haiston
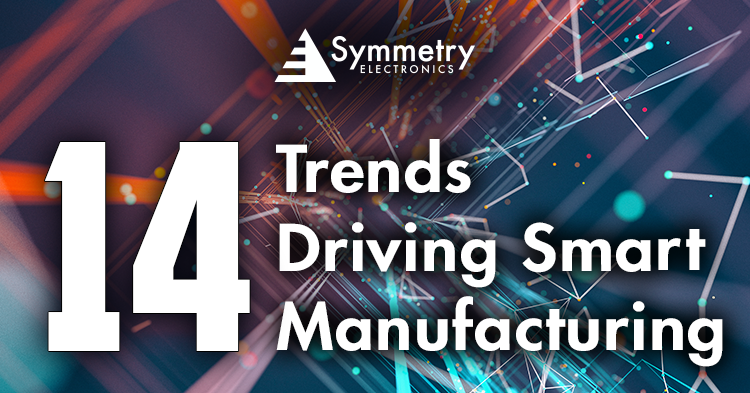
Did you know that the industrial manufacturing industry has the highest adoption of internet of things (IoT) technology among all industries? Smart manufacturing is the integration of physical and digital within factories, warehouses, and other supply chain functions to optimize supply/demand requirements. Manufacturing is made intelligent through the utilization of IoT technology like sensors, cameras, and other connected devices. IoT implementation in industrial settings is one of the pillars of industry 4.0 and stands to revolutionize the global manufacturing market.
14 Major Reasons to Adopt IoT in Manufacturing
Valued at $249.56 billion in 2021, Fortune Business Insights predicts that the global smart manufacturing market is expected to grow to $658.41 billion by 2028. Smart manufacturing practices have helped factories achieve productivity gains of 17–20% but Microsoft’s recent report, IoT Signals, has outlined the top 14 reasons companies are adopting IoT in their manufacturing processes:
- Quality & Compliance
- Industrial Automation
- Production Flow Monitoring (Discrete Only)
- Production Planning & Scheduling
- Supply Chain & Logistics
- Plant Safety
- Product-as-a-Service (Process Only)
- Connected Field Service/New Business Models
- Condition-Based Monitoring & Service
- Worker Safety
- ‘Connected’ Product Engineering
- Condition-Based Predictive Maintenance
- Process Optimization
- Overall Equipment Effectiveness
Levels of Smart Manufacturing
According to Microsoft, 27% of the manufacturing companies they surveyed still see IoT integration as too overwhelming and complex to integrate. However, there are multiple levels of automation integration in smart factory processes that can be gradually implemented to ensure a smooth transition into industry 4.0 standards.
Level 1 begins with connected data. This is the level where sensors, signals, machines, and other connected devices enable real-time capabilities.
Level 2 focuses on integrating the benefits of analyzed data gathered from the connected devices in level one to into preventive insights to help companies reduce downtime caused by equipment failures. This practice is known as predictive analytics.
Level 3 incorporates machine learning (ML) technologies with predictive analytics from the previous stage into prescriptive analytics. Prescriptive analytics can help isolate variables and settings historical production data to optimize overall production optimization.
Level 4 involves artificial intelligence (AI) driven automation functions to actually recommend and deploy actionable insights that it analyzes from production data. Talk about removing the guesswork. Full AI-Driven automation is still in development but is the ultimate goal of smart factory manufacturing.
Developing a Smart Manufacturing Environment
If you’re interested in propelling your manufacturing process into industry 4.0, our team of Applications Engineers is available to guide you through the complex path of automated integration. Our Applications Engineers are experts in connected devices, wireless technologies, and IoT solutions and can provide you with invaluable insights into developing intelligent manufacturing practices. Consultation is free and available throughout your entire design cycle. Contact Symmetry Electronics today!