- Home
- Symmetry Blog
- Isolation Tech 101, Part 4: Analog Isolators | Symmetry Blog
Isolation Tech 101, Part 4: Analog Isolators | Symmetry Blog
About Symmetry Electronics
Established in 1998, Symmetry Electronics, a Division of Braemac, is a global distributor of electronic components and systems. Combining premier components and comprehensive value-added services with an expert in-house engineering team, Symmetry supports engineers in the design, development, and deployment of a broad range of connected technologies.
Exponential Technology Group Member
Acquired by Berkshire Hathaway company TTI, Inc. in 2017, Symmetry Electronics is a proud Exponential Technology Group (XTG) member. A collection of specialty semiconductor distributors and engineering design firms, XTG stands alongside industry leaders TTI Inc., Mouser Electronics, and Sager Electronics. Together, we provide a united global supply chain solution with the shared mission of simplifying engineering, offering affordable technologies, and assisting engineers in accelerating time to market. For more information about XTG, visit www.xponentialgroup.com.
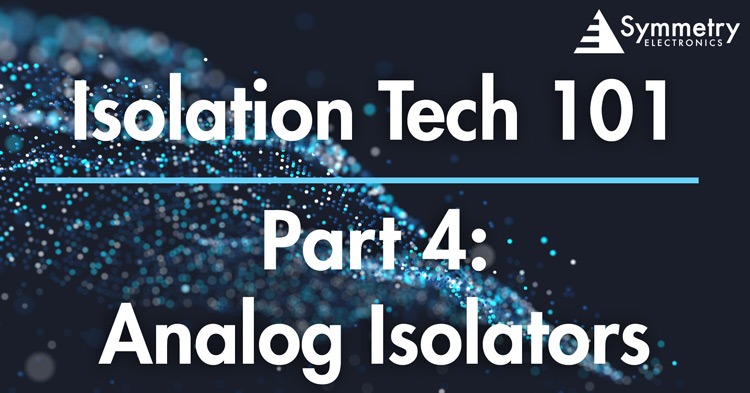
Many considerations come into play when choosing the right isolator for your application. In a new blog series from Symmetry Electronics, we will be covering the different types of isolators available. In Part 1, we covered digital isolators, in Part 2, we covered isolated gate drivers, and in Part 3, we covered Isolated Analog to Digital Converters. For Part 4, we will be providing an overview of Analog Isolators, how they work, and when to use them.
Keep reading to learn everything you need to know about analog isolators.
Analog Isolators
In: Analog signal
Out: Amplified analog signal
Whether you call them signal isolators, signal converters or signal interfaces, these useful process instruments solve important ground loop and signal conversion challenges every day. Just as important, they are called upon to do a whole lot more. They can be used to share, split, boost, protect, step down, linearize and even digitize process signals. This guide will tell you many of the important ways signal isolators, converters and interfaces can be used, and what to look for when specifying o
Why the Need for Signal Isolation?
The need for signal isolation began to flourish in the 1960s and continues today. Electronic transmitters were quickly replacing their pneumatic predecessors because of cost, installation, maintenance and performance advantages. However, it was soon discovered that when 4-20mA (or other DC) signal wires have paths to ground at both ends of the loop, problems are likely to occur.
The loop in question may be as simple as a differential pressure (DP) transmitter sending a 4-20mA measurement to a receiver, such as a recorder. But when the voltages (V) at the two ground points are different, a circulating, closed current (I) path is formed by the copper wires used for the 4-20mA signal and the ground. When this happens, an additional and unpredictable amount of current is introduced into the loop, which distorts the true measurement. This current path, known as a ground loop, is a very common source of signal inaccuracies.
A ground loop forms when three conditions are present:
- There are two grounds
- The grounds are at different potentials
- There is a galvanic path between the grounds
To remove the ground loop, any one of these three conditions must be eliminated. The challenge is, the first and second conditions are not plausible candidates for elimination. Why? Because you cannot always control the number of grounds, and it is often impossible to just “lift” a ground.
The ground may be required for the safe operation of an electronic device. It’s also possible that the ground exists because the instrument is in physical contact with
the process which, in turn, is in physical contact with the ground. From a practical standpoint, you cannot reach into the earth and regulate the voltage at these permanent ground points.
So what can be done? Use a signal isolator to “break” the galvanic path between the two grounds. When the conductive path between the differential voltages is broken, a current cannot form. So even though there are two grounds and different voltages at each ground, there is no current flow. The ground loop has been eliminated.
The Importance of Breaking the Galvanic Path
The first and foremost duty of an isolator is to break the galvanic path between circuits that are tied or “grounded” to different potentials. A galvanic path is defined as a path in which there is a direct electrical connection between two or more electrical circuits that allow current to flow. Breaking this galvanic path can be accomplished by any number of means including electromagnetic, optic, capacitive, inductive and even acoustic methods.
With most industrial measuring equipment, the two prevalent methods chosen for galvanic isolation are optical and transformer.
What is Optical Isolation?
Optical isolation uses light to transfer a signal between elements of a circuit. The opto-coupler or opto-isolator is usually self-contained in a small compact module that can be easily mounted on a circuit board.
An optical isolation circuit is comprised of two basic parts: a light source (usually a LED- Light Emitting Diode, acting as the transmitter) and a photo-sensitive detector (usually a phototransistor, acting as the receiver). The output signal of the opto-coupler is proportional to the light intensity of the source. The insulating air gap between the LED and the phototransistor serves as the galvanic separation between the circuits, thus providing the desired isolation between two circuits at different potentials.
Optical isolation has better common-mode noise rejection, is usually seen in digital circuits, is not frequency sensitive, is smaller, and can sometimes provide higher levels of isolation than transformer isolation.
What is Transformer Isolation?
Transformer isolation, often referred to as electromagnetic isolation, uses a transformer to electromagnetically couple the de- sired signal across an air gap or non-conductive isolation gap. The electromagnetic field intensity is proportional to the input signal applied to the transformer. Transformers are very efficient and fast at transferring AC (alternating current) signals. Since many process control signals are DC, they must be electrically “chopped” into an AC signal so they can pass across the transformer. Once passed, they have to be rectified and amplified back into the de- sired DC signal output.
Where do I find the best Analog Isolators for my needs?
The Silicon Labs Si8920 is a galvanically isolated analog amplifier ideal for measuring voltage across a current shunt resistor or for any place where a sensor must be isolated from the control system. Our amplifier family offers low voltage and differential input while providing higher performance, reduced variation with temperature and age, tighter part-to-part matching, and longer lifetimes compared to other isolation technologies.
The very low signal delay of the Si8920 allows control systems to respond quickly to fault conditions or changes in load. Low offset and gain drift ensure accuracy is maintained over the entire operating temperature range. Exceptionally high common mode transient immunity enables the Si8920 to deliver accurate measurements even in the presence of high power switching, such as in motor drive system or inverter applications.
The Si8920 isolated amplifier utilizes our proprietary isolation technology and supports up to 5.0 kVrms withstand voltage per UL1577. The output is a differential analog signal amplified by either 8.1x or 16.2x.
Features:
- Low voltage differential input
- ±100 mV and ±200 mV options
- Low signal delay: 0.75 µs
- Input referred offset: 0.2 mV
- Gain error: <0.5%
- Excellent drift specifications
- 1 µV/°C offset drift
- 60 ppm/°C gain drift
- Nonlinearity: 0.1 % full-scale
- Low noise: 0.10 mVrms over 100 kHz bandwidth
- High common mode transient immunity: 75 kV/ µs
- Compact packages:
- 16-pin wide-body SOIC
- 8-pin surface mount DIP
- -40°C to 125°C
- AEC-Q100